Multiple Communication Channels
Our technical formulation capabilities combined with flexible manufacturing systems ensure your flooring specifications are met precisely, while our 24-hour response commitment eliminates procurement delays that can impact your project timelines.
Direct Phone Line
Immediate technical consultation for urgent manufacturing questions
WhatsApp Business
Real-time production updates and sample coordination
LinkedIn Connect
Professional network and industry insights sharing
Comprehensive Customization Services
From surface textures to structural specifications, our customization capabilities help you create distinctive product lines that differentiate your brand in competitive markets.

Design Flexibility
Our extensive design capabilities transform your creative vision into marketable flooring solutions, helping you establish unique product positioning that commands premium pricing.
- Custom wood grain and stone texture development
- Proprietary color matching and trend forecasting
- Surface finish optimization for specific applications
- Pattern registration and embossing customization
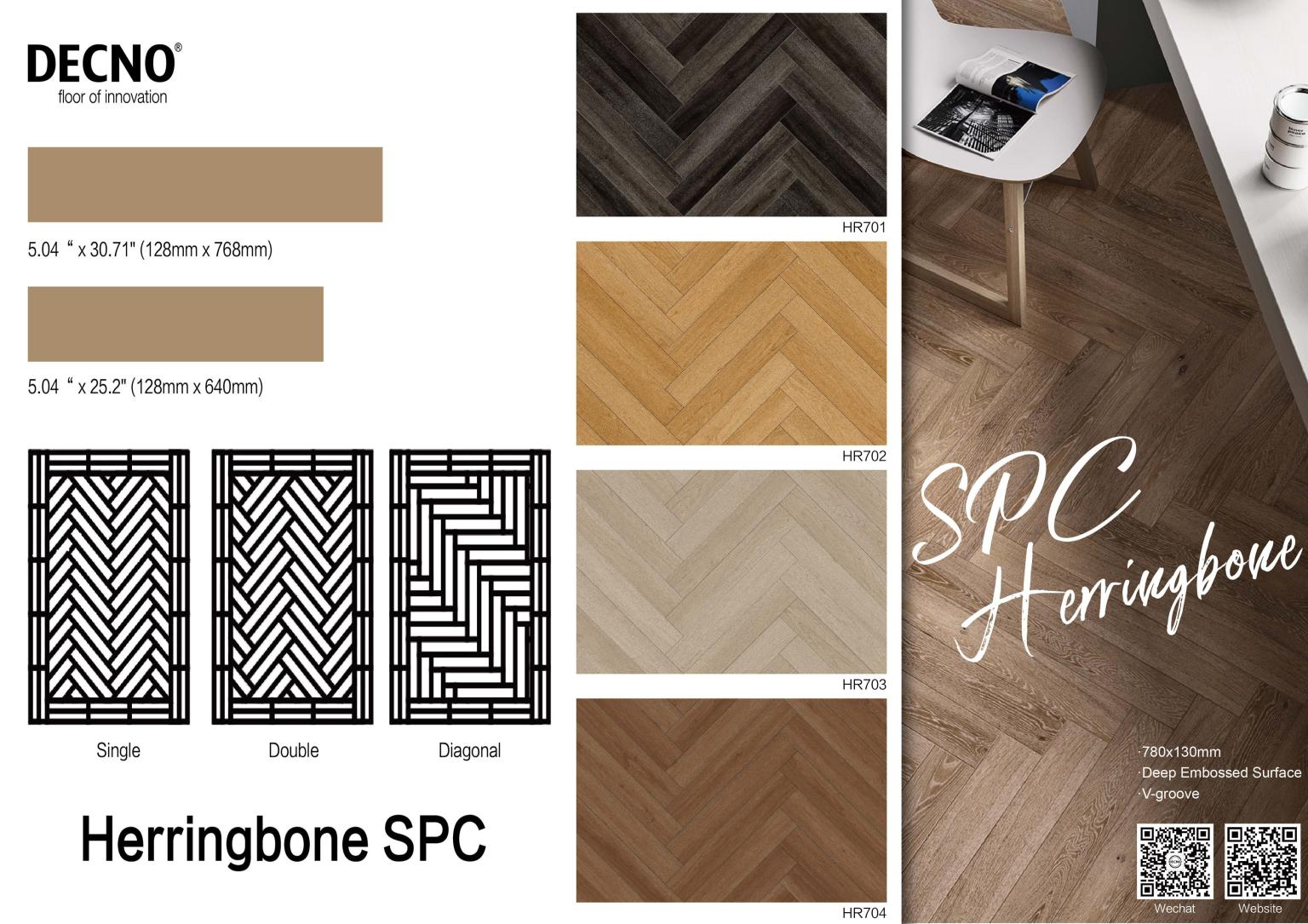
Structural Engineering
Technical customization ensures your products meet specific performance requirements while optimizing cost efficiency, reducing warranty claims and customer complaints.
- Thickness range from 3mm to 8mm
- Click-lock, dry-back, and loose lay systems
- Integrated sound dampening solutions
- Enhanced wear layer for high-traffic applications

Sample Development
Our comprehensive sampling process accelerates your product development timeline while ensuring final production matches your expectations, reducing market entry delays.
- 5-7 day express sample turnaround
- Complete performance testing documentation
- Market-ready packaging prototypes
- Installation guide development
Quality & Delivery Assurance
Our integrated quality management system and streamlined production scheduling deliver the reliability your business demands, eliminating the uncertainty that can compromise your market commitments.

Advanced Testing Laboratory
In-house formulation lab ensures consistent product performance across different production runs, eliminating quality variations that can impact your customer satisfaction ratings and repeat business.
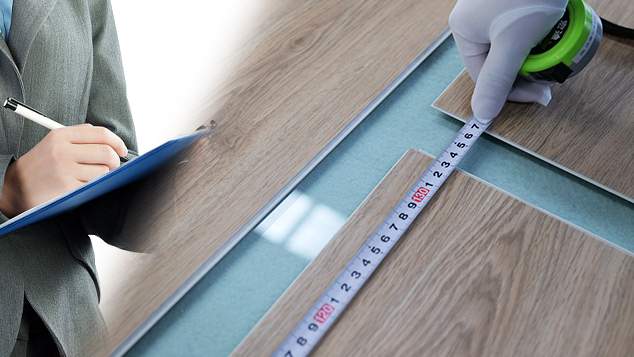
Precision Manufacturing
State-of-the-art extrusion lines with real-time monitoring maintain dimensional accuracy within ±0.1mm, providing the installation consistency your contractors need to complete projects efficiently.
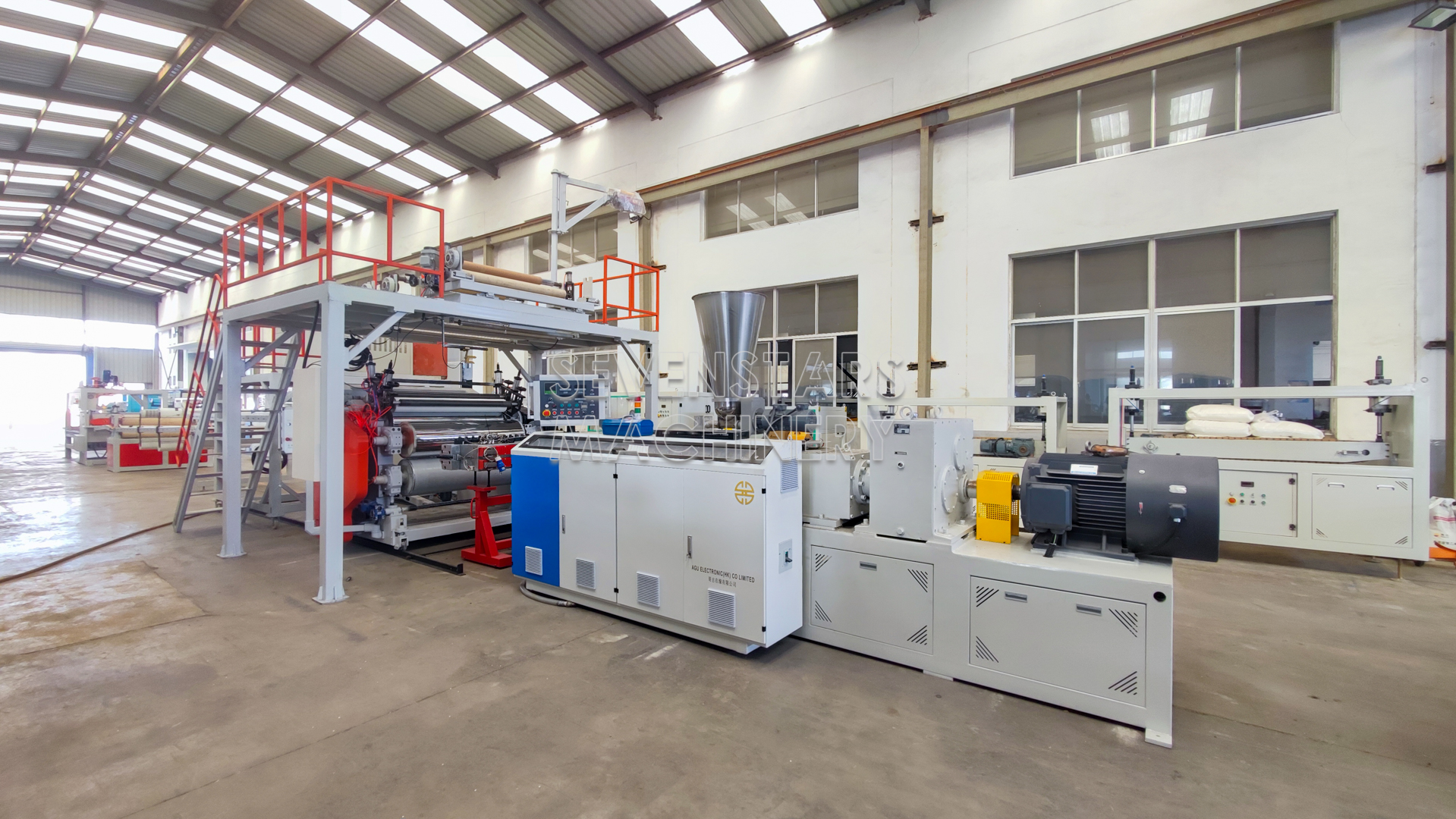
Guaranteed Delivery Schedule
98% on-time delivery rate with 15-20 day regular production cycles protects your inventory planning and ensures your sales commitments are met without costly rush orders or stockouts.

Third-Party Verification
Independent quality verification and pre-shipment inspection services provide the documentation and confidence your procurement processes require for supplier approval and risk management.
Success Stories by Industry
Our specialized manufacturing capabilities have solved complex flooring challenges across multiple industries, delivering measurable improvements in project efficiency, cost management, and end-user satisfaction.
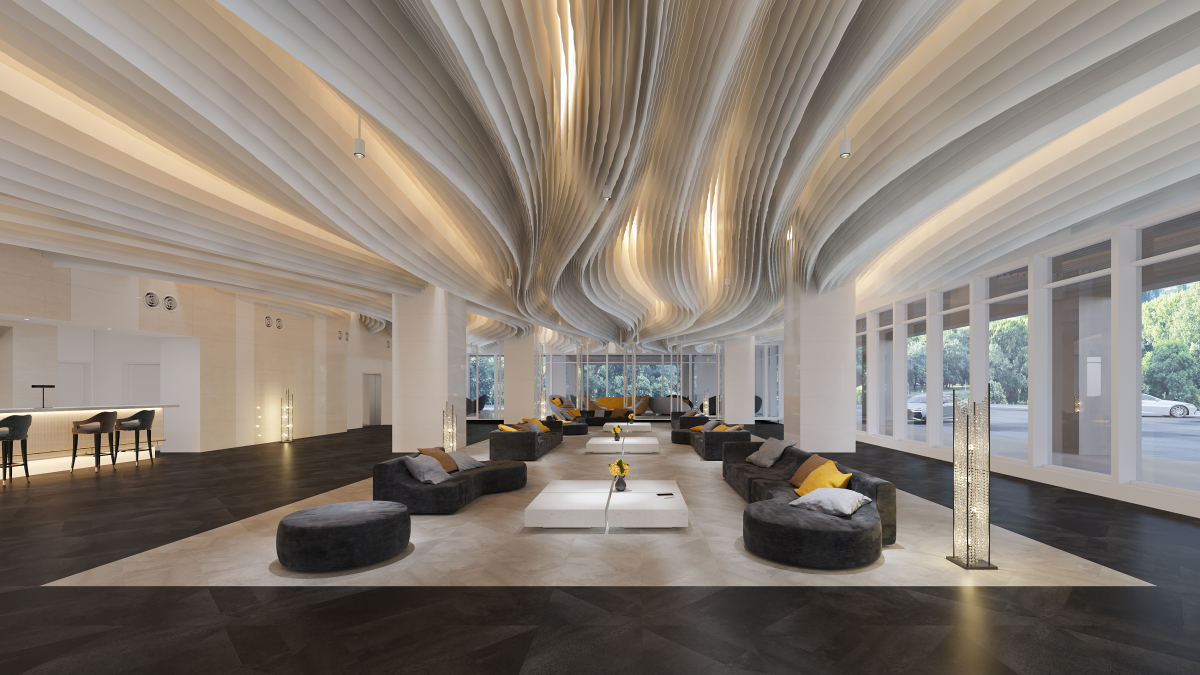
Luxury Hotel Chain - North America
Custom 6mm SPC with enhanced acoustic backing reduced installation time by 40% across 15 properties. Our moisture-resistant formulation eliminated callback issues in high-traffic areas, saving $180K in maintenance costs annually.
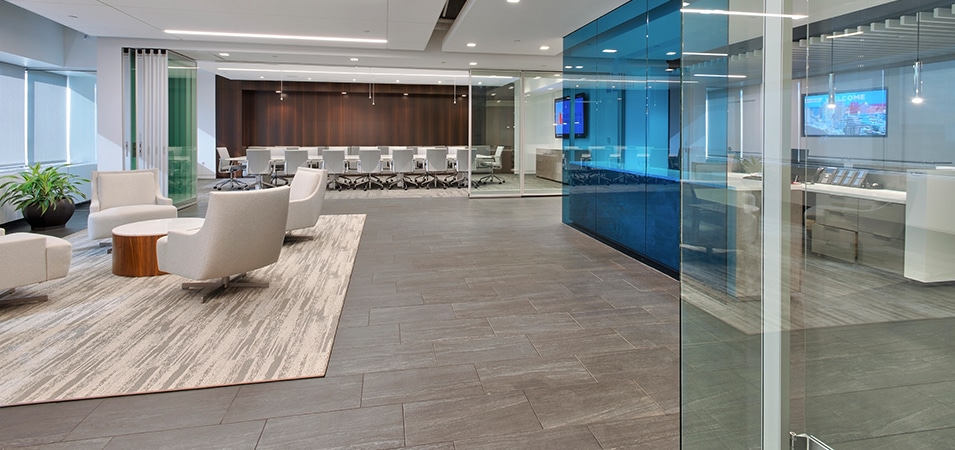
Fortune 500 Office Complex
Coordinated delivery of 280,000 sqft across 8 buildings with zero installation delays. Our custom wear layer specification provided 25% longer lifespan, reducing replacement frequency and total cost of ownership.
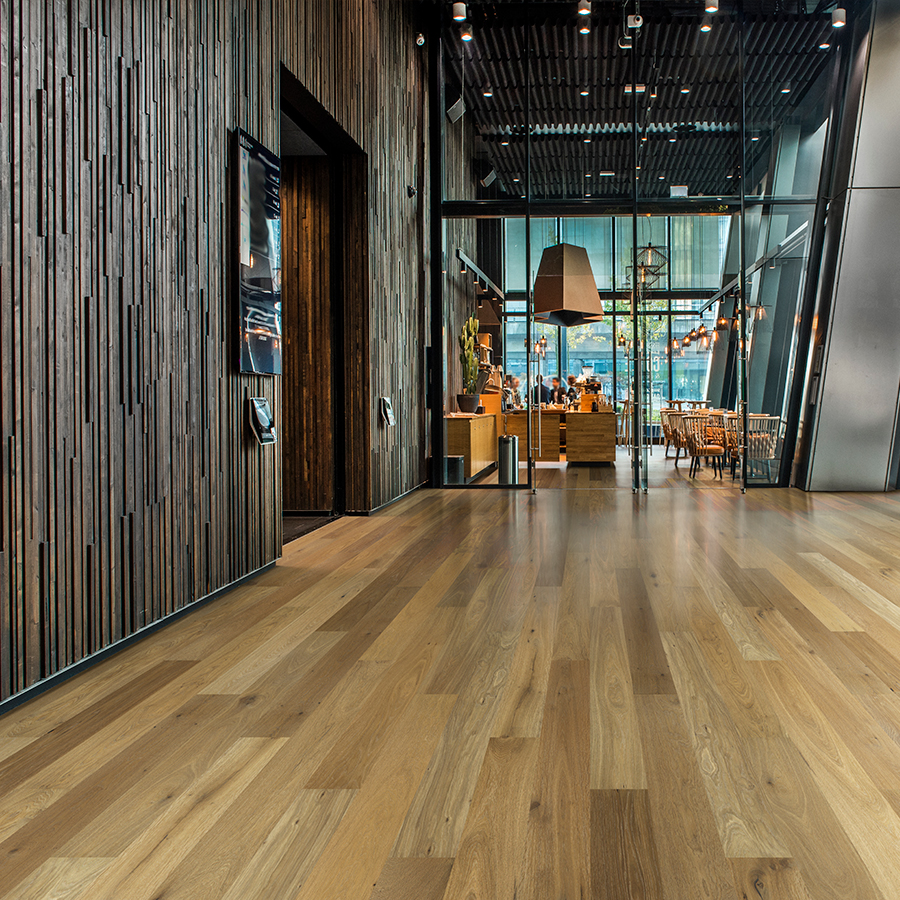
National Retail Brand Rollout
Standardized 4mm LVT solution across 120 locations with consistent color matching and performance. Our flexible minimum order quantities enabled phased rollouts without excess inventory costs.
What Our Partners Say
Direct feedback from procurement professionals who have experienced the operational advantages of partnering with Morton's manufacturing capabilities.
"Morton's lab-developed formulations solved our moisture issues in basement installations. Their technical support prevented $50K in warranty claims on our first major project."
"15-day delivery windows that actually hold true. Morton's production scheduling eliminated our inventory management headaches and improved our cash flow significantly."
"The only supplier who delivers batch-consistent color matching across multiple orders. Our contractors finally stopped complaining about shade variations mid-project."
"Morton's compliance documentation made our FDA and CARB approvals seamless. Their attention to certification details saved us months of regulatory delays."
Certifications & Export Compliance
Comprehensive certification portfolio ensures your imports meet all regulatory requirements, eliminating customs delays and compliance risks that can impact your business operations.
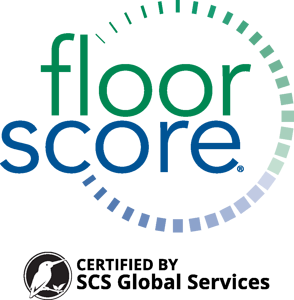
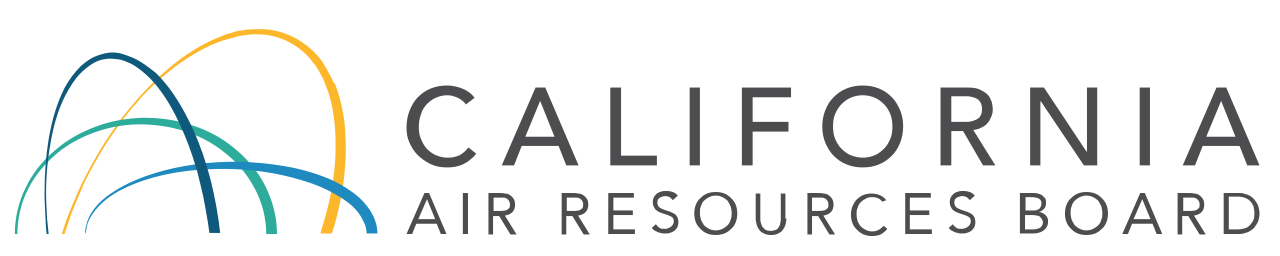



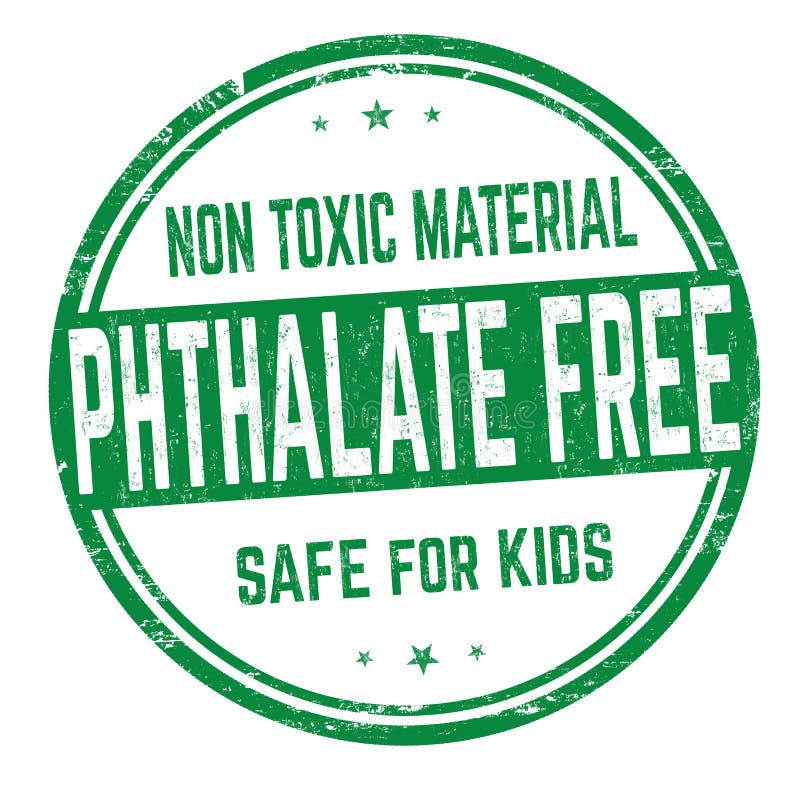
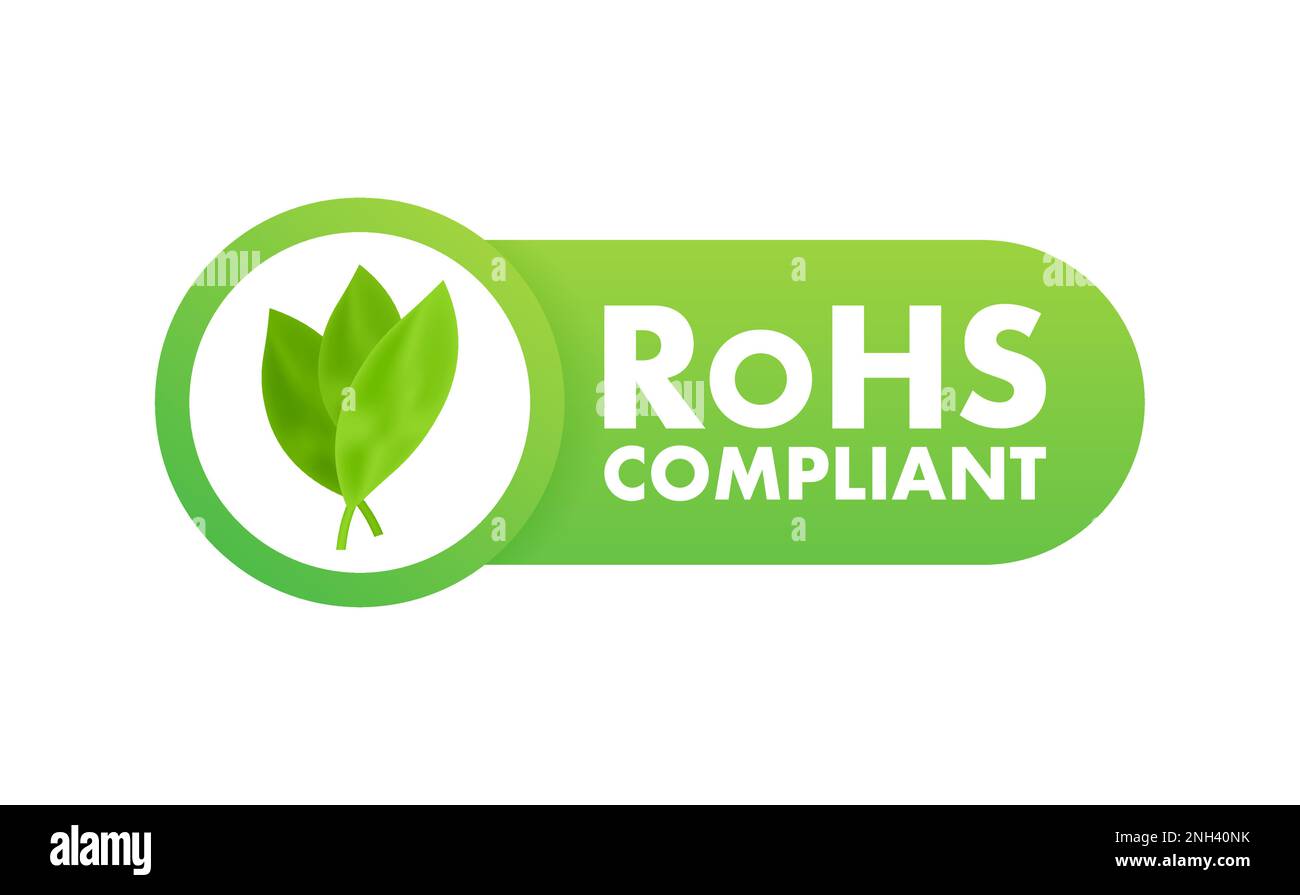
Visit Our Manufacturing Facility
Located in China's advanced manufacturing zone with direct access to major shipping ports, ensuring efficient logistics for your global supply chain requirements.
Start Your Manufacturing Partnership
Connect with our technical team to discuss your specific flooring requirements and discover how our manufacturing capabilities can solve your sourcing challenges.
Why Choose Morton?
Our advanced formulation laboratory and flexible production systems eliminate the common frustrations of international flooring sourcing - inconsistent quality, delayed deliveries, and complex compliance issues.
- Custom formulations for market-specific requirements
- Flexible minimum orders (300 sqm single color)
- 98% on-time delivery performance
- Comprehensive quality documentation
- 24-hour technical response guarantee
Frequently Asked Questions
Technical and operational answers to the most common questions from international flooring procurement professionals.